Shell Heat Exchanger
Advantages:
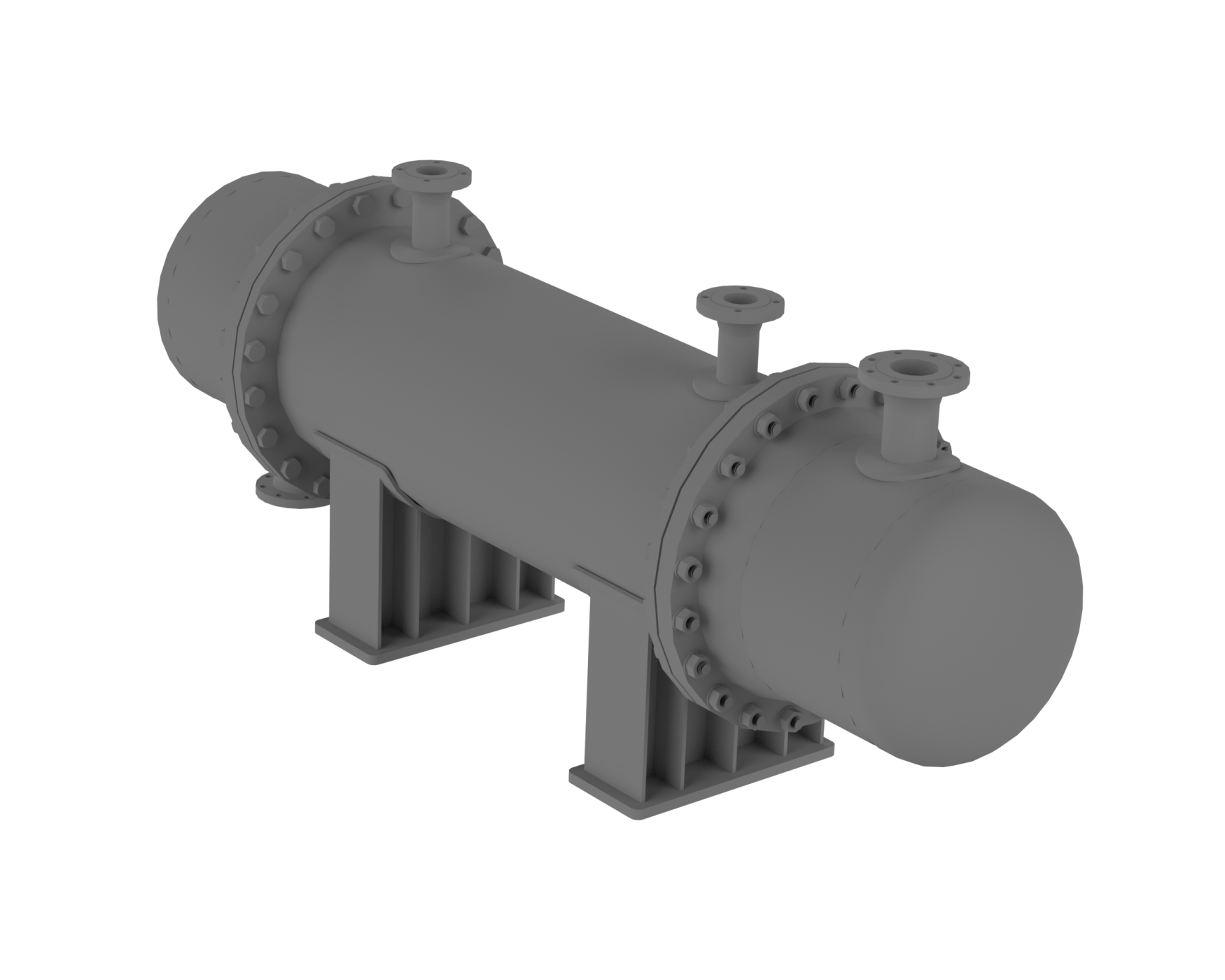
What is a shell and tube heat exchanger?
Shell and tube heat exchanger is the most popular type of heat exchanger. It consists of a cylindrical shell and a tube bundle mounted inside. In a shell and tube exchanger, heat is transferred between two fluids. One cold fluid flows inside the tubes (the tube side), while the second hot fluid flows in the shell over the outside of the tubes (the shell side).
Heat transfer coefficient
The heat transfer efficiency of a shell and tube heat exchanger refers to how well heat is transferred in relation to the pressure drop. Overall heat transfer coefficient refers to how well heat is conducted through a series of resistant media. It depends on the thermal properties of a medium, hydrodynamic, thermal boundary conditions, and the characteristics of its flow. The heat transfer rate in the heat exchanger, in general, depends on the material through which heat is transmitted. The effect of material on the heat transfer rate is called thermal conductivity, which is a measure of a material's ability to transfer heat.
Shell and tube heat exchangers design should be carried out in such a way to maximize heat transfer while minimizing pressure drop and meet other design goals such as withstanding high fluid pressures, corrosion, resistance to contamination, repairing, and cleaning. Shell and tube heat exchangers can be used for a variety of applications. For instance, in the petrochemical industry which is covered by standards from TEMA, Tubular Exchanger Manufacturers Association, for the power industry, and as power plant condensers.
Shell and tube heat exchanger parts
- tube sheet
- tubes
- baffle plates
- tube bundle with straight tubes
- shell inlet and outlet
- tube inlet and outlet
- tie-rods
Rendering odor control
In different types of meat rendering plants, it is important to have a system to deal with bad odor smells. Shell and tube heat exchangers can be used in meat and fish rendering plants for treating hot vapor and gases after the disc dryers and cookers. Heat transfer causes a condensation process from vapor to liquid. Non-condensable gases are separated and subjected to further purification. Condensate liquid is easy to pump away, and the amount of the non-condensable gases is incomparably smaller than the vapor volume coming from the disc dryer or the rendering cooker. For cooling of the hot gases, cold water is used. CIP cleaning can be installed.
Waste heat recovery
Shell and tube heat exchangers can be used in meat and fish rendering plants as a waste heat recovery machine from the drying or cooking process. Saturated steam for the animal by-products processing costs money. Thanks to the installation of a such waste heat system, it is possible to make savings which will decrease the price of used steam for the process.